Home > Products > Port Crane > Ship Loader
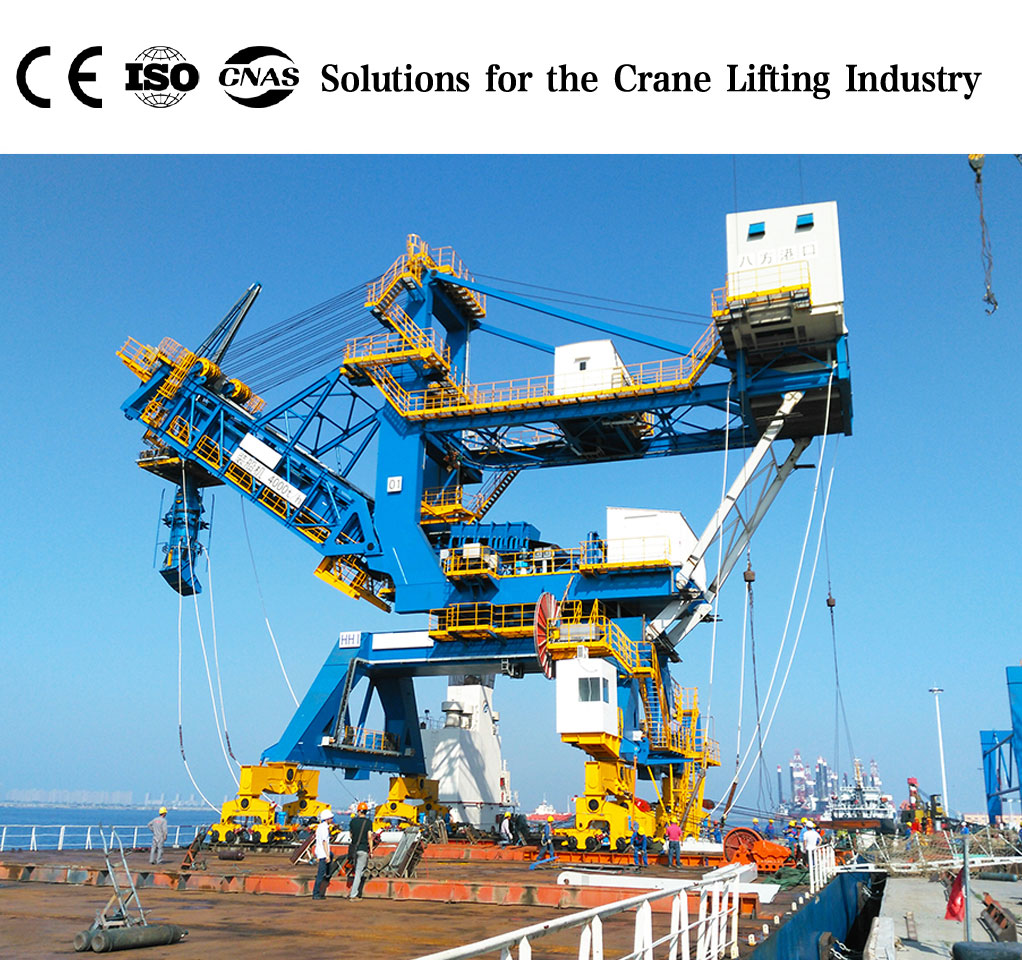
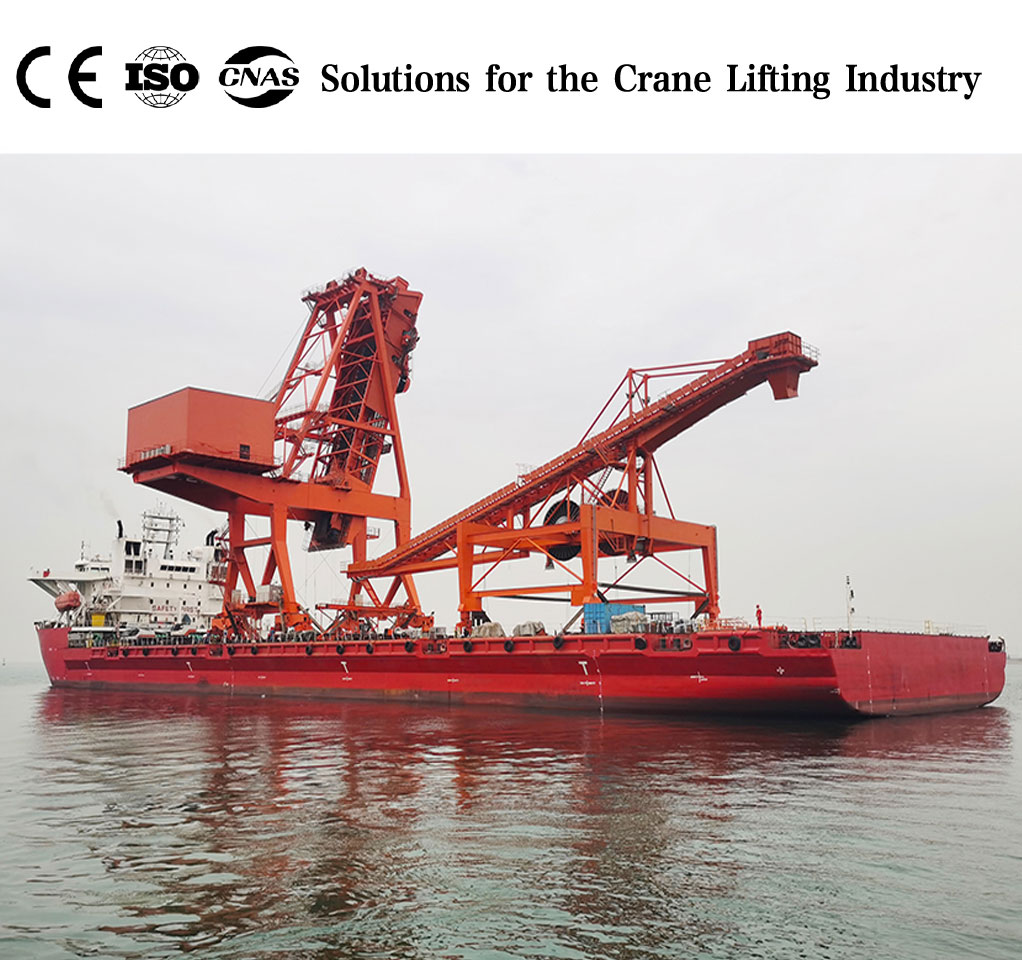
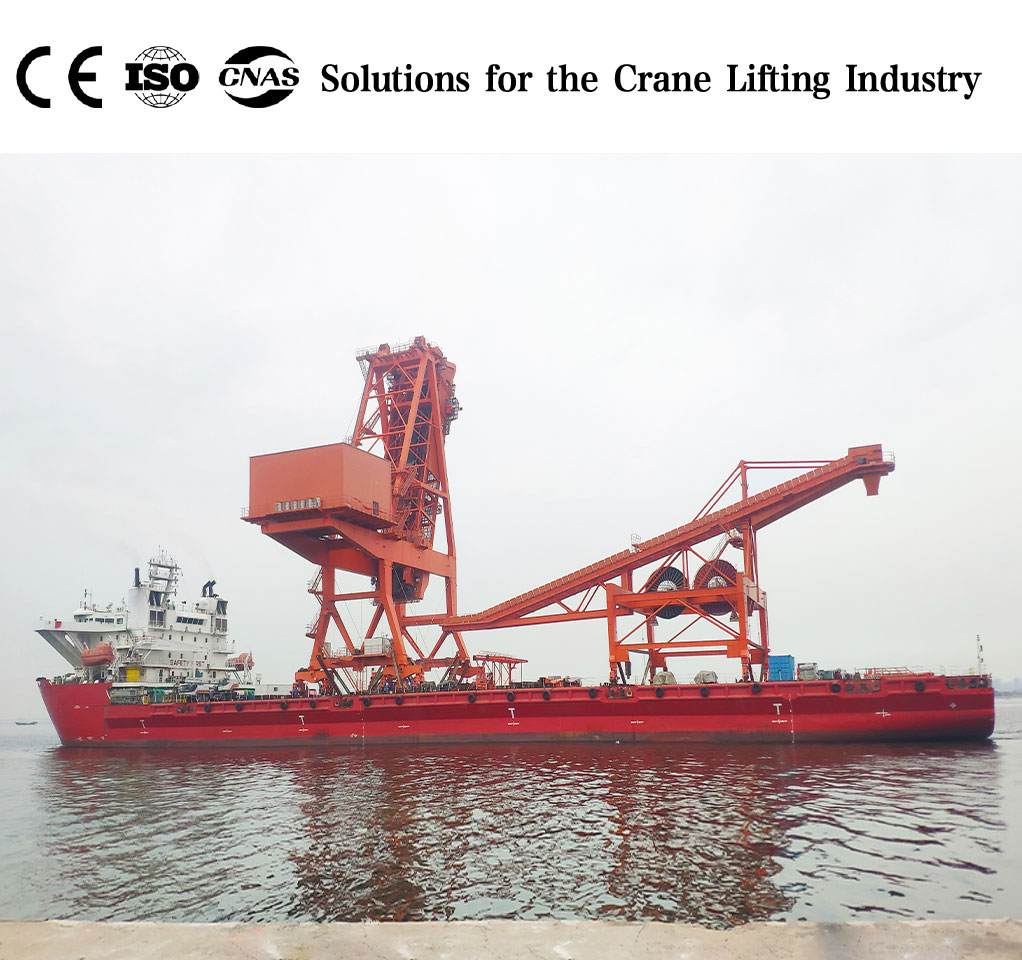

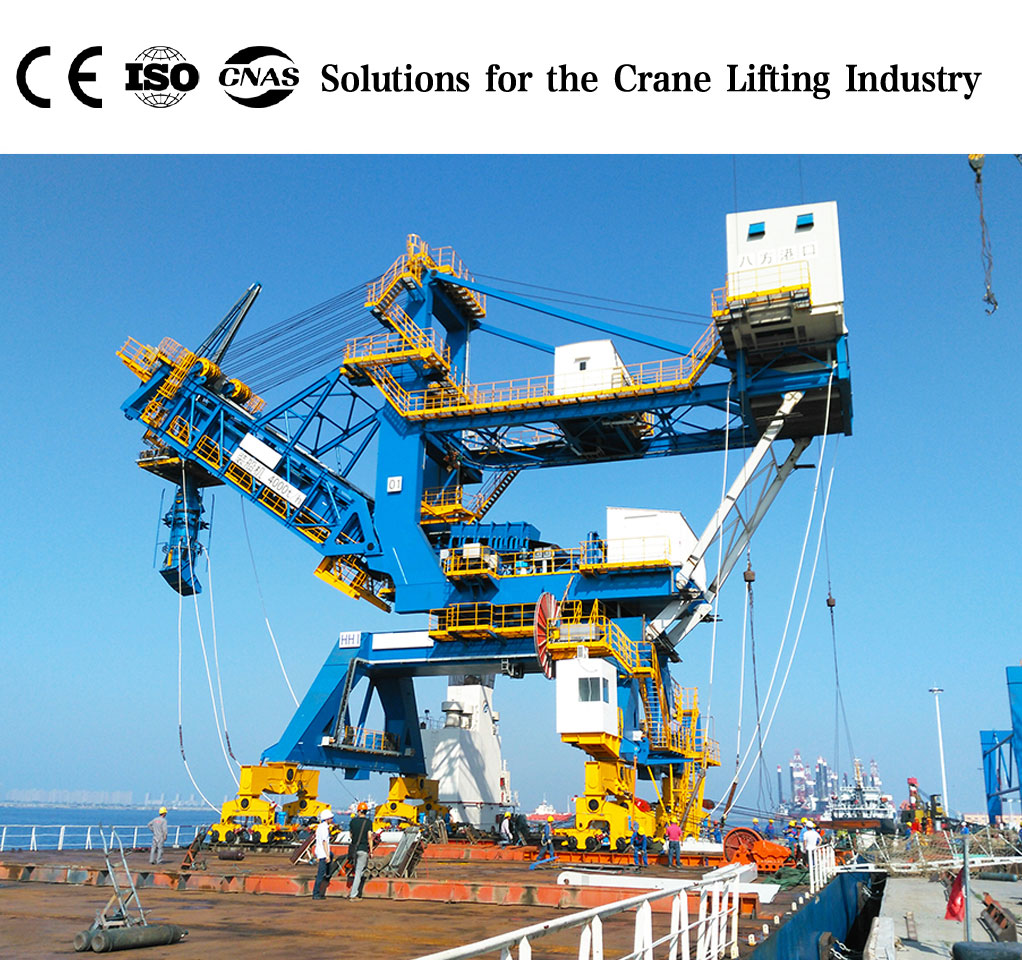
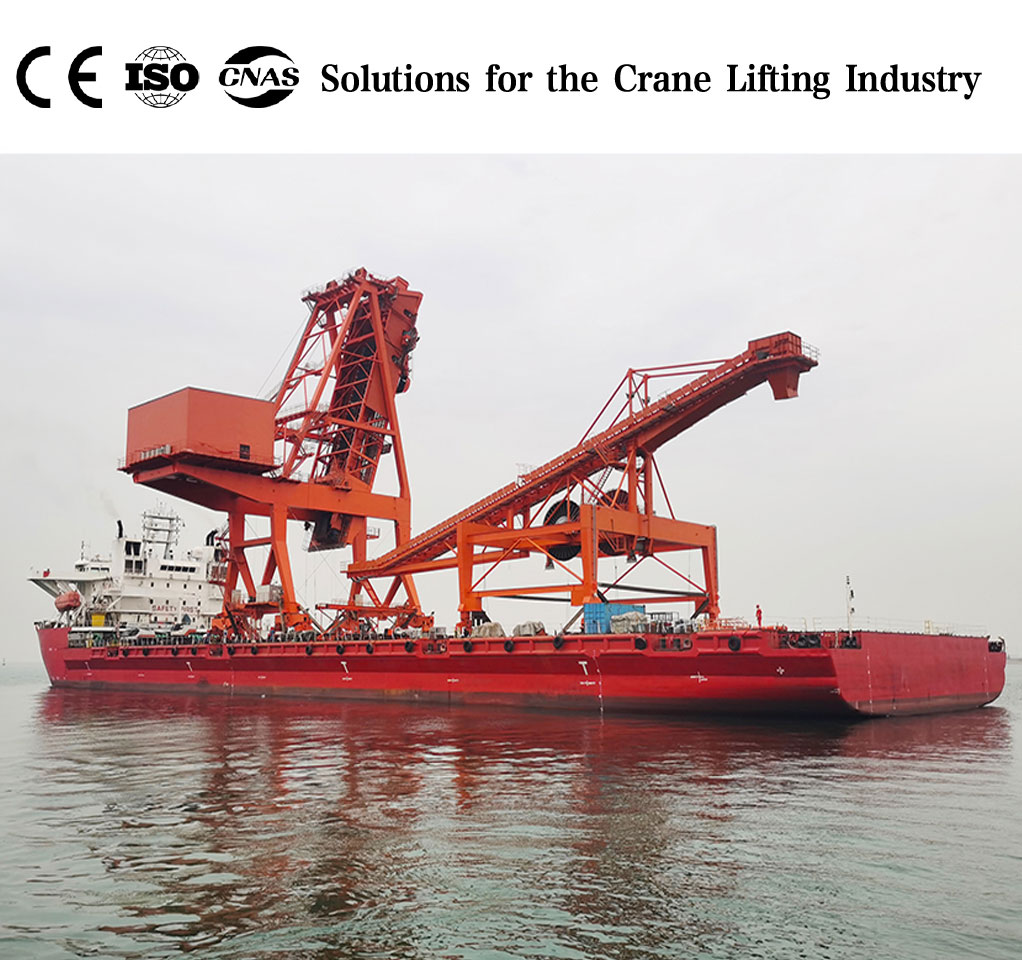
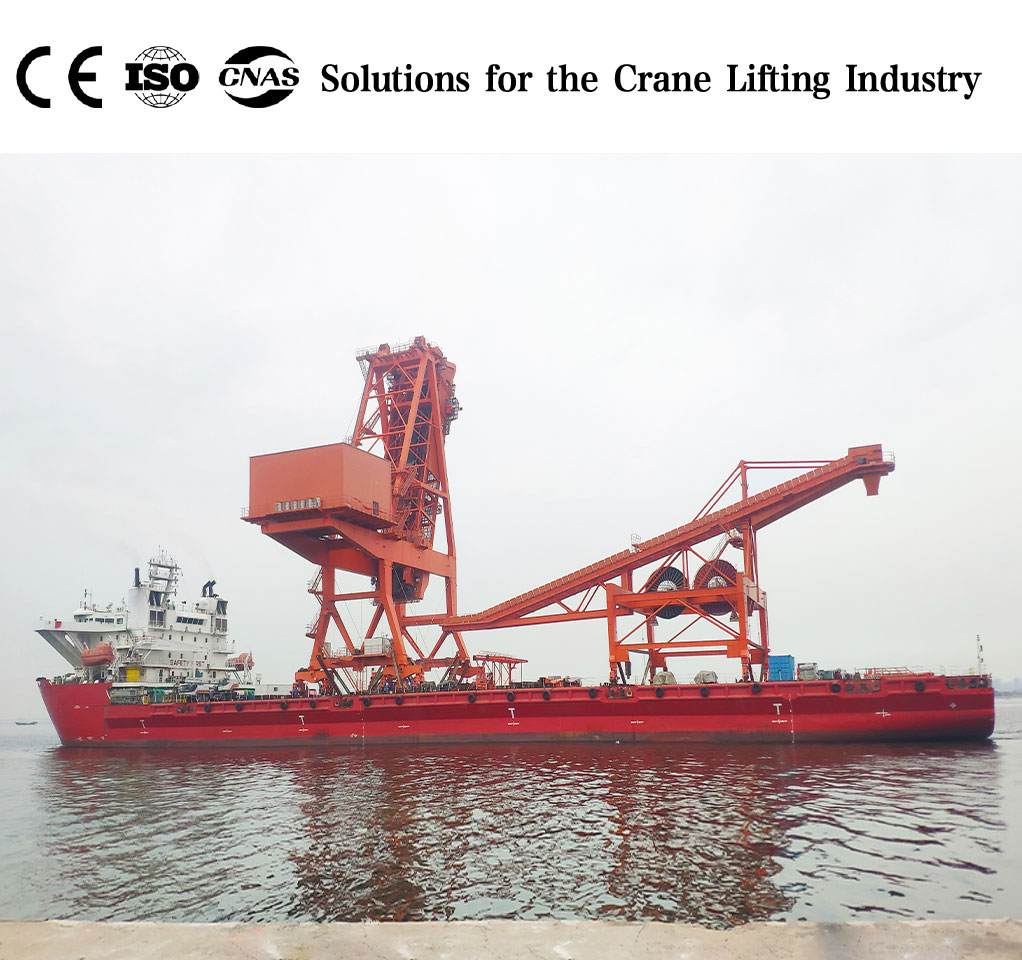

Ship Loader
Ship Loader - Efficient and reliable bulk material handling is critical for smooth port operations. That's why Yangyumech provide expertly designed ship loaders that seamlessly integrate with your port infrastructure and ensure optimal performance for your specific requirements.
Loading capacity: 1,000 t/h to 20,000 t/h
Vessel size: 5,000 DWT to 350,000 DWT
Systems specifically designed to your unique requirements
Description
A shiploader is a large machine used for continuously loading bulk solid materials such as iron ore, coal, fertilizers, grains and/or material in bags onto ships or barges. These machines are located in ports and jetties to facilitate bulk material exportation. Generally shiploaders are engineered to suit specific project requirements. Those requirements often include: port design, material characteristics, loading capacity, vessel type.
When selecting and designing a ship loader, the quality and properties of the bulk material, local conditions, performance parameters and environmental requirements play a decisive role.
With these aspects in mind, our engineers determine the most effective and cost-efficient handling principle while minimising operational and maintenance requirements. The customised loading system must fit in your port infrastructure and match current and future vessel sizes. Whether it’s coal, aggregates, mineral compounds, or other bulk materials, our ship loading systems deliver robust performance to keep your operations running smoothly.
Features
Rail-mounted mobility
Our rail-mounted ship loaders include a tripper car supplying material to be conveyed which is generally located either between the rails or beyond the landside running rail of the ship loader. Depending on specific customer and/or environmental requirements, we are able to shield the tripper car and pier conveyor belt from the external environment with an enclosed pier bridge.
Rotating or swiveling functionality
For applications in which vessels are loaded on a finger pier with double-sided berthing, we are able to equip our ship loaders with a rotating or swiveling function. In this instance, the tripper car and pier conveyor belt are located between the rails of the ship loader, with the advantage that the ship loader and tripper car can all run on one rail. For piers with unilateral berthing and vessels with predominantly upright loading hatches, a non-rotating ship loader with a shuttle boom is employed. In this instance, the tripper car is installed on a separate pier bridge beyond the landside running rail of the ship loader and runs on independent rails.
Fixed or stationary solutions
Fixed ship loaders are generally employed in instances where environmentally hazardous material is to be loaded. A significant advantage of these machines is the excellent encapsulation of the feed route so that there is virtually no release of material into the environment – together with protection of the feed material from the elements. The drawback of these machines is that, in many instances, the vessel must be moved, either forward or back, for the purposes of loading into a different hatch.
Technical Data
Ship Loader-------------------------------------Technical Specification |
||||
Items |
MS30 |
MS100 |
MS180 |
Unit |
Rate productive capacity |
300 |
1000 |
1800 |
t/h |
Limit capacity |
360 |
1200 |
2000 |
t/h |
Bulk cargo |
Coke |
Bulk cement |
Coal |
|
Ship size |
5000 |
5000 |
5000 |
DWT |
Width of belt conveyor |
1000 |
1400 |
1400 |
mm |
Speed of belt conveyor |
2.5 |
2.42 |
3.5 |
m/s |
Chute extending length |
8.15 |
19.5 |
19.5 |
m |
Chute extending length speed |
9.3 |
4 |
3.6 |
m/min |
Components
-
-
Electric Trolley
Hoist trolley usually installed on the heavy duty bridge crane or gantry crane as a lifting mechanism. It has a simple structure and light weight. It’s mainly used in general hoisting, loading and unloading operations in machinery manufacturing workshops, warehouses, assembly and hydro-power station maintenance.
-
Main beam
The main beam is the crane's main load-bearing component, and the running track for the electric hoist. It is a triangular beam is weld by a support frame(welded by angle steel and other section steel) and an I-beam. The two sides of the span are designed with saddles connected to the outriggers, and there are rectangular steel plate connecting flanges. There are buffers at both ends of the main beam to ensure the safe operation of the trolley on the main beam.
-
Steel Lifting Spreader Beam
Steel Lifting beam can be used to lift and move a wide range of industrial loads. The hooks on both ends can be adjusted to any location you want. Lifting beam is a good choice when the headroom is limited and restricts the use of overhead rigging in the application. Lifting beam is usually made from a beam and a single lifting point at the top with several lift points at the bottom.
-
Wheel Set
The wheel set is a mechanical device consisting of a wheel and a shaft, a bearing and a bearing housing. The crane wheel set is generally used for the vehicle to support the crane and the load, and at the same time, the crane is allowed to perform the reciprocating running operation on the specified track.
-
Crane Cab
The crane cab is the workplace of the crane operator and it undertakes a crucial role. The design of the cab fully considers the comfort and safety of the operator. It has a good view so that the operator can clearly observe the surrounding environment and operating conditions.
-
Control model
Can use control handle with pendant line, wireless remote control, or cabin control.
-
industry
case Center
our service
-
Equipment Manufacture
The annual output is more than 900,00 units, with more than 100 sets of advanced equipment, and the full product line automation rate reaches 80% .
-
Construction Management
Control project delivery, cost and quality ,from design to end of building ,according to customer's technical requirements
-
Technical Trainning
Provide comprehensive training, including equipment structure and principle training, installation specification training, etc., also 24H after-sales technical supporting, to ensure equipment stable operation on site
-
Spare Parts/Fast delivery
We provide over 220 types of cranes and their related products, saving customers’ purchasing time.